I haven’t updated this blog for a couple years now. We’ve used the trailer for three trips. The first was the shakedown- we got up into British Columbia, Canada in the summer of 2017, but it got too hot and we came home. Then we went to Arizona, New Mexico, and a little into southern Colorado in September 2018. That was fun. But the big trip was up through British Columbia and Yukon, Canada to Alaska.
We got to Denali National Park. We were lucky on the weather. For those of you who aren’t from the U.S., Denali is known for having the tallest mountain in North America and a huge area of truly wild country. There is a single road from the entrance to Wonder Lake, a bit over 90 miles in. Normally visitors aren’t allowed to take their cars beyond the entry area, but if you have a reservation for the Teklanika campground you can go there. It’s 29 miles in. You leave your car there, and you can either walk or ride the buses that come along virtually every half hour. We went to Teklanika.
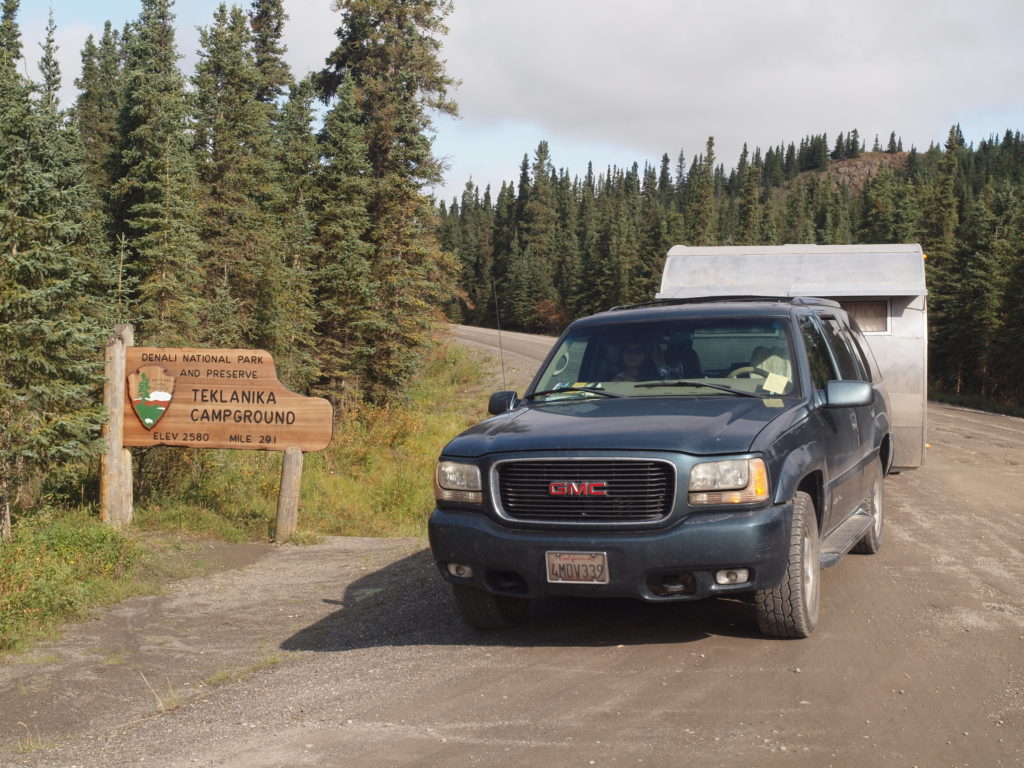
Fewer than half the people who visit Denali actually see the Mountain. (People who live there rarely say “Denali”, or its old name of “Mount McKinley. It’s just “the mountain”.) It’s so tall it makes its own weather. According to the ranger we talked to, normally Denali park gets 14 inches of precipitation a year. Half falls as rain and half as snow. In the month before we got there, Denali got 18 inches of rain. The road was closed and the bulldozers just got it opened two days before we got there. We rode the bus out to Eilsen visitor center, which is the best view of the mountain. That day it looked like this:
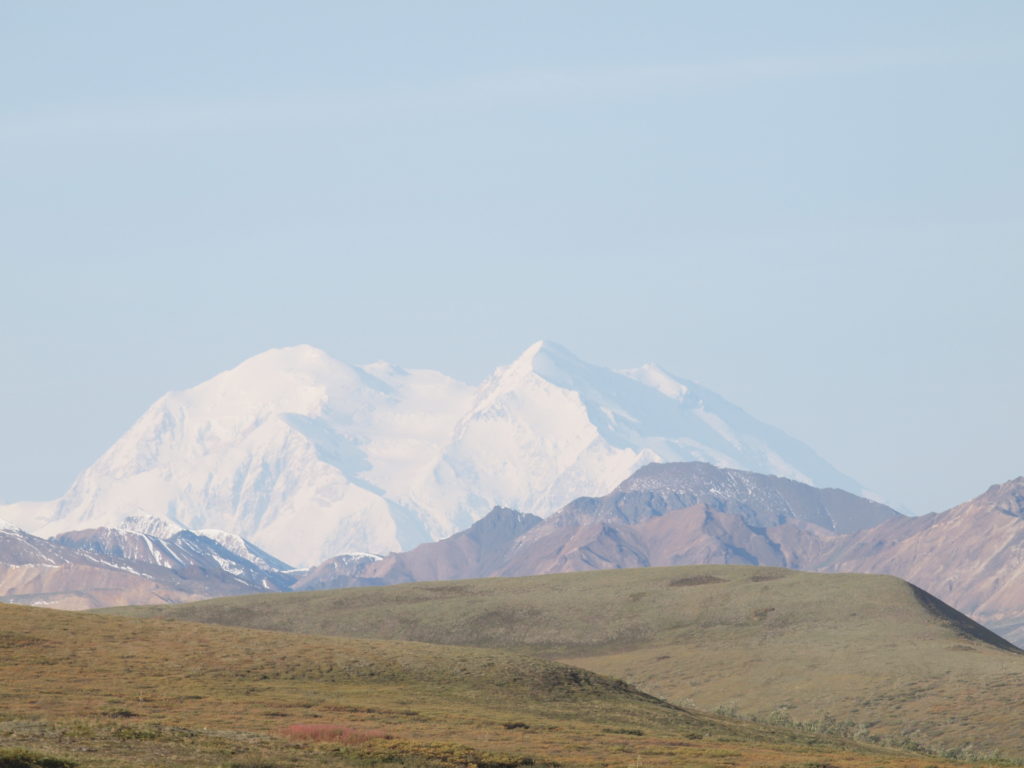
And the next day it was overcast. We were there for six days and it never again was clear like this.
We had intended to go to the coast, which is beautiful in a different way, but there were several major wildfires in the areas we wanted to go. My wife has serious asthma, and if we drove past a major wildfire that trip would end in the nearest emergency room.
We drove the Denali Highway back. Horrible dirt road- the bouncing did some damage to the trailer but nothing I can’t fix. This picture was taken somewhere around here.
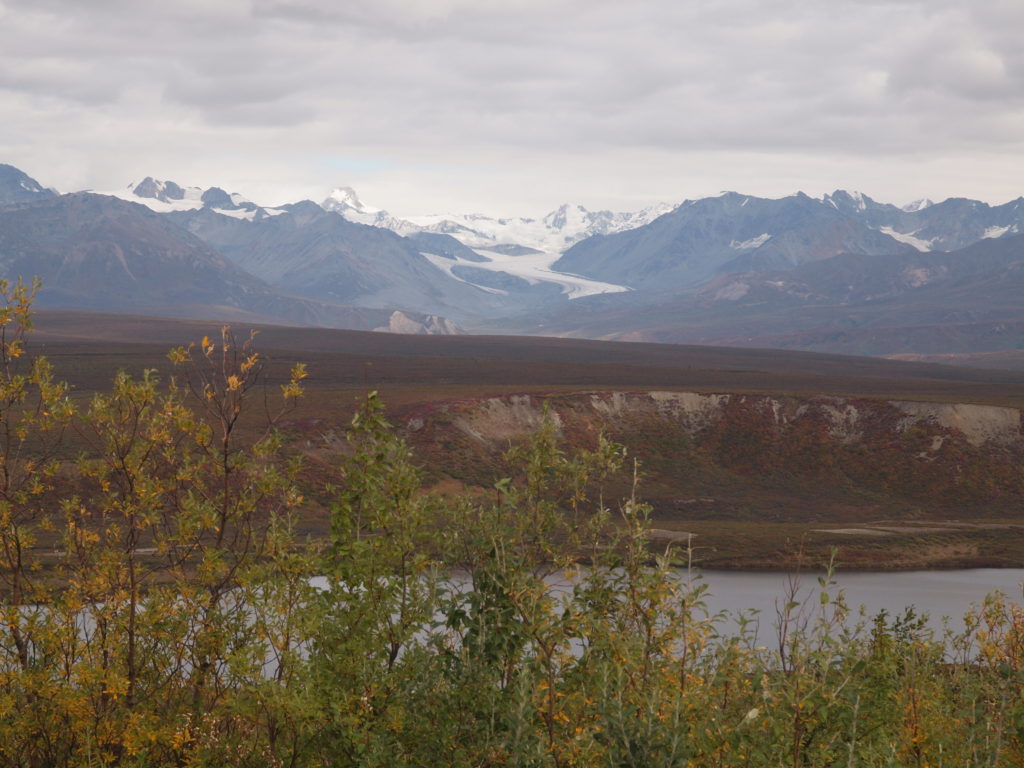
The land in this picture belongs to the Ahtna first nations tribe. (Formerly known as American indians, which if you know geography is pretty silly. They mostly prefer to be called first nations.)
Here’s what’s special about this area, and much of Alaska. If you’ve never been there it’s hard to imagine how wild this is. Imagine you were in great shape and had excellent outdoor skills. Further imagine you had a helicopter available to drop you whatever you needed where and when you needed it, so you could go over mountains and cross rivers and marshes. To keep things simple, when you cross a road you immediately go far enough to the side so you don’t cross that road again as it winds back and forth.
If you walk north from here, in eight or ten miles you’ll hit a major highway. In Alaska that means a two-lane paved highway. As you cross it, look left and right. You might see a sign, and you might see one or two cars or trucks as you cross, assuming you cross in daylight during the summer. You probably won’t see a building or secondary road. In another 150 or so miles you’ll cross another similar road. In about another 300 miles you’ll reach the Arctic Ocean without seeing another road or building.
If you walk west, in 110 miles or so you’ll cross another similar road. Then in 400 miles you’ll stand on the shores of the north Pacific ocean. With luck you might see some walruses.
If you walk south, in 75 miles or so you’ll cross another road. You’ll cross in a more populated area, so you probably will see a building or two as you cross. In another 100 miles or so you’ll see the Pacific Ocean, either in Prince William Sound or the Copper River Delta.
If you walk east, in 75 miles or so you’ll cross another road. In 40 miles or so you’ll cross another. 30 or 40 miles after that you’ll be in Canada, but you’ll have to walk another 100 miles or so to find a road and people who can tell you that.